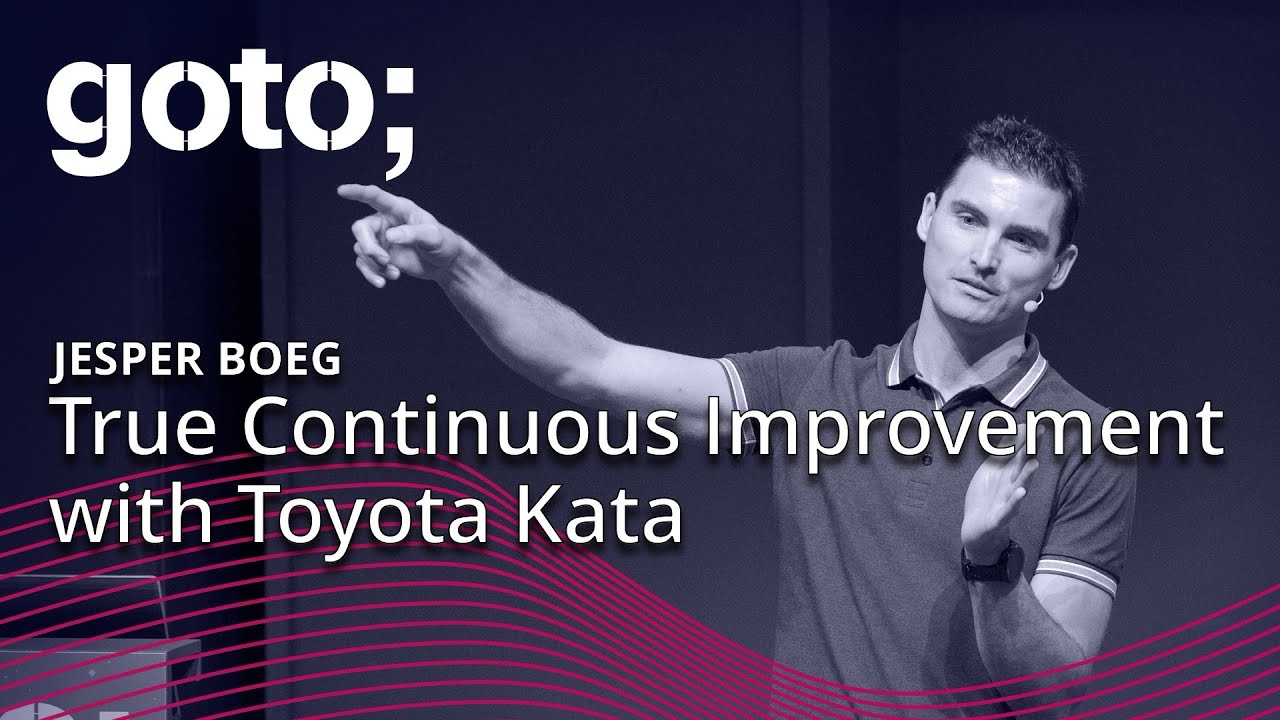
Your Potential is much Bigger than You Think – True Continuous Improvement with Toyota Kata!
You need to be signed in to add a collection
Well, it seems most of us got it wrong. While the Lean manufacturing community were busy copying everything from “Andon Buttons” to “Work Cell Layouts" from Toyota, Agile Coaches (myself included) convinced companies that “Burndown Charts”, “Product Owners” and “Sprint Review meetings” were all part of essential best practices that would solve their problems and make them successful. In 2009 Mike Rother published a book with the strange name “Toyota Kata”. Reading that was a deciding moment personally and a wake-up call for many consultants across the world. The basic message was that though we can achieve short term success by copying tools and practices, long term success comes from a focus on the underlying goal and establishing a culture that systematically works to improve in that direction across all layers of the organization. But what is the Agile version of “One-by-one-flow” that governs most improvement work at Toyota – the Agile “True North” that goes beyond specific practices and tools? How does Toyota Kata translate into a development context where variability is much higher, managers are not experts and the flow of value is counted in days and not seconds? In this presentation I will share the experiences from the last 4 years with Toyota Kata. Primarily the last year helping Bankdata roll-out Toyota Kata across all layers of the 700 people organization. Where did we fail, what adaptions were made, what results did we achieve and why is it both more powerful and more difficult than any of us believed? Come along and be inspired and maybe even a bit provoked – chances are you will never look at improvement the same way again.
Transcript
Well, it seems most of us got it wrong. While the Lean manufacturing community were busy copying everything from “Andon Buttons” to “Work Cell Layouts" from Toyota, Agile Coaches (myself included) convinced companies that “Burndown Charts”, “Product Owners” and “Sprint Review meetings” were all part of essential best practices that would solve their problems and make them successful.
In 2009 Mike Rother published a book with the strange name “Toyota Kata”. Reading that was a deciding moment personally and a wake-up call for many consultants across the world. The basic message was that though we can achieve short term success by copying tools and practices, long term success comes from a focus on the underlying goal and establishing a culture that systematically works to improve in that direction across all layers of the organization.
But what is the Agile version of “One-by-one-flow” that governs most improvement work at Toyota – the Agile “True North” that goes beyond specific practices and tools? How does Toyota Kata translate into a development context where variability is much higher, managers are not experts and the flow of value is counted in days and not seconds? In this presentation I will share the experiences from the last 4 years with Toyota Kata. Primarily the last year helping Bankdata roll-out Toyota Kata across all layers of the 700 people organization. Where did we fail, what adaptions were made, what results did we achieve and why is it both more powerful and more difficult than any of us believed?
Come along and be inspired and maybe even a bit provoked – chances are you will never look at improvement the same way again.